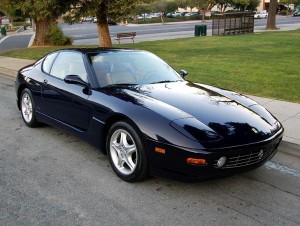
Ferrari 456M 1998-2003 Workshop Repair & Service Manual (COMPLETE & INFORMATIVE for DIY REPAIR) ☆ ☆ ☆ ☆ ☆
* COMPLETE, Absolutely No Missing Pages!
* Official Service INFORMATION You Can Count On!
* Customer Satisfaction GUARANTEED!
This high QUALITY official manual for 1998–2003 Ferrari 456M (Type F116M) is 100 percents COMPLETE and INTACT, no MISSING, CORRUPT pages, sections to freak you out! This manual is exactly as described. It is in the cross-platform PDF document format so that it works like a charm on all kinds of devices.
FORMAT: PDF
LANGUAGE: English Italian German French
SIZE/PAGE: 401 MB / 508 Pages
OS: Windows/Mac OS X/Linux/Android/iOS
1998 1999 2000 2001 2002 2003 Ferrari 456M (Type F116M)
INSTANT DELIVERY: A download link will be sent to you instantly after payment. Simply click on the link and save it to your computer. You can use this Manual as long as you wish with no restrictions.
CUSTOMER SATISFACTION: If there is ANY kind of problem with the item you purchased, just drop a quick email. Within HOURS the issue shall be taken care of.
PRINTABLE MANUAL WITH DIAGRAMS: Just print the manual out and start to work. You can also use the manual with your Tablet/Laptop in your garage.
REFUND/EXCHANGE POLICY: We sell high QUALITY products only. However if you encounter any problems with the item you purchased, another replacement link will be sent to you. If we’re at fault, you will get 100 percents refund.
Buy ☆THE BEST MANUAL ON THE INTERNET☆ from responsible seller and get instant download now without uncertainty or surprise.
This highly detailed workshop service repair manual for download contains virtually everything you will ever need to repair, maintain, rebuild, refurbish or restore Ferrari 456M 1998-2003. All diagnostic and repair procedures and gives you access to the same information that professional technicians and mechanics have. You can view and print out the complete repair procedures with this workshop service repair manual Download – you do not need to be skilled with a computer.
EXCERPTS:
Starting
• As the engine turns the ECU has to recognise engine timing from the sequence of signals that are sent from the revolution and timing sensors to synchronise injection and ignition.
• During this phase with a speed of more than 30 rpm, the ECU, in order to facilitate
starting, operates all the electro-injectors simultaneously and for a time which only depends on coolant temperature.
• After this first injection, once engine timing is known, the sequential and timed control of the injection starts and the electro-injectors are controlled for the injection time calculated by the ECU.
• This enrichment follows the trend shown in the graph of Fig. 20 and is active until the coolant temperature reaches 60°C.
• Still during the starting phase, apart from this enrichment, the ECU also adjusts the injection time in relation to the number of engine revolutions.
• As shown in the graph of Fig. 21, as the rpm increases, the injection time decreases
to avoid sending an excessive amount of fuel to the cylinders.
Note: the starting phase is recognised by the ECU for speeds between 30 and 640 rpm.
Active Diagnosis
• The active tests that can be made by the SD-1 Diagnosis System are:
1 – Electro-injectors.
2 – Idling speed actuator.
3 – Secondary air valve and air pump relay.
4 – Anti-evaporation valve.
5 – Oil/water electric fan relay.
6 – Self-learnt value cancelling.
Note: the M5.2 version DOES NOT allow the self-learnt parameters to be cancelled or reset by cutting the ECU off; during this step a diagnosis step has been added, for resetting the ECU. Thus, for a good engine operation, cancel the self-learnt parameters whenever the actuators are replaced or a new carburation is to be carried out.
Automatic cycle
•This cycle controls the actuators starting from a detailed procedure, for detecting possible system malfunctioning.
•The cycle should be performed completely in case of anomalies difficult to be trouble-shot, to check progressively the Motronic system and its relevant adjustments step-by-step.
Help messages
• Whenever the word “help” appears at the bottom of the screen it is possible to display Help messages concerning the operation being performed or the screen data, or even the parameter reference valves, by pressing the “F1” key.