INSTANT DOWNLOAD (add to cart)
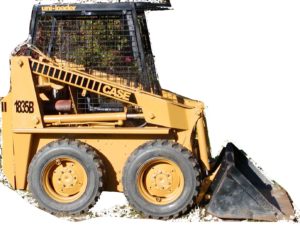
Case 1835B Uni-Loader Workshop Repair & Service Manual
1,038 pages, bookmarked, Searchable, Printable, high quality PDF
Case 1835B Uni-Loader Service Manual.pdf; 1,038 pages
Complete digital official shop manual contains service, maintenance, and troubleshooting information for the Case 1835B Uni-Loader. Diagnostic and repair procedures are covered in great detail to repair, maintain, rebuild, refurbish or restore your Case 1835B Uni-Loader like a professional mechanic in local service/repair workshop. This cost-effective quality manual is 100% complete and intact as should be without any missing pages. It is the same factory shop manual used by dealers that guaranteed to be fully functional to save your precious time.
This manual for Case 1835B Uni-Loader is divided into different sections. Each section covers a specific component or system and, in addition to the standard service procedures, includes disassembling, inspecting, and assembling instructions. A table of contents is placed at the beginning of each section. Pages are easily found by category, and each page is expandable for great detail. It is in the cross-platform PDF document format so that it works like a charm on all kinds of devices. You do not need to be skilled with a computer to use the manual.
EXCERPT:
18358 UNI-LOADER
TABLE OF CONTENTS
Safety Rules, Service Manual Introduction, and Torque Specifications .. 1001
Maintenance and Lubrication .. 1082
General Engine Specifications -188 Diesel Engine .. 1010
Detailed Engine Specifications -188 Diesel Engine … 1027
General Engine Specifications- 148 Spark Ignition Engine .. 1110
Detailed Engine Specifications- 148 Spark Ignition Engine .. 1129
2 ENGINES
Engine Removal and Installation, Engine Accessories (Air Cleaner, Muffler, Ether Injection System, Radiator) .. 2000
188 DIESEL ENGINE
Engine Diagnosis .. 2001
Engine Tune-Up … 2002
Cylinder Head, Valve Train, and Camshaft … 2015
Cylinder Block, Sleeves, Pistons, and Rods … 2025
Crankshaft, Bearings, Flywheel, and Oil Seals .. 2035
Oil Pump .. 2045
Cooling System … 2055
Engine Lubrication .. See Section 2555
148 SPARK IGNITION ENGINE
Engine Tune-Up … 2102
Cylinder Head, Valve Train, and Camshaft … 2115
Cylinder Block, Sleeves, Pistons, and Rods … 2125
Crankshaft, Bearings, Flywheel, and Oil Seals .. 2135
Oil Pump … 2145
Cooling System … … 2155
Engine Lubrication- 188 Diesel Engine .. 2555
3 FUEL SYSTEM
Engine Controls, Fuel Line, Fuel Tank, and Hand Pr!mer Pump. 3001
Fuel Filters- 188 Diesel Engine … 301G
Fuel Injection Pump- 188 Diesel Engine … 3012
Fuel Injectors- 188 Diesel Engine .. 301’3
Carburetor- 148 Spark Ignition Engine .. 311’2′
4 ELECTRICAL
Electrical System Troubleshooting … 4002
Wiring Diagrams … 4003
Fuel Gauge and Warning Lamps .. 4004
Battery .. 4005
Starter … 4006·
Alternator .. 4007
Distributor Ignition System … 4008
6 POWER TRAIN
Hydrostatic System Troubleshooting . 6002
Hydrostatic System Diagrams and Operation … 6003
Piston Pump .. 6004
Hydrostatic Motor … 6005″
Hydrostatic Controls .. 6006
Drive Sprockets, Chains, and Axle Housings … 6007
Drive Coupling .. 6010
Wheels and Tires .. 6011
7 BRAKES
Parking Latch … 7001
8 HYDRAULICS
Hydraulic System Specifications, Diagrams, Troubleshooting,
Pressure Checks, Flowmeter Tests . 8002
Cleaning the Hydraulic System … 8003
Equipment and Charge Pump .. 8004
Loader Control Valve .. 8005
Auxiliary Control Valve .. 8006
Backhoe Control Valve .. 8007
Cylinders .. 8009
9 MOUNTED EQUIPMENT
Loader … 9001
Backhoe … 9002
ROPS Canopy, Operators Seat … 9003
Decals, Painting, and Noise Control .. 9005
…
Crankshaft Inspection And Installation
STEP 115
Measure the main bearing journals to see if the journals are worn. Measure the front and rear of each journal. Use undersize bearing liners if the diameters are smaller than 2.6230″ (66.6242 mm). 0.002″ (0.0508 mm) undersize bearing liners can be used without grinding the journals to keep the specified bearing clearance.
NOTE: Grind the crankshaft journals undersize 0.010″ (0.254 mm), 0.020″ (0.508 mm) or 0.040″ (1.016 mm) if the crankshaft journals are worn more than 0.002″ (0.0508 mm). See Section 1129 of the Service Manual for the grinding dimensions.
STEP 116
Measure the main bearing journals, again, 90 degrees from the first measurements (Step 115) for out-of-round. Grind the journals and use undersize liners if the out-of-round is more than 0.0005″ (0.0127 mm).
STEP 117
Measure the connecting rod journals for taper.
Measure the front and rear of each journal. Grind the journals if the taper is more than 0.002″ (0.0508 mm).
STEP 118
Check the rod journals again, 90 degrees from the first measurements (Step 117) for out-of-round.
Grind the journals if the out-of-round is more than 0.001″ (0.0254 mm).
STEP 119
Remove the crankshaft gear if the gear is damaged or worn. Use a puller to remove the gear.
STEP 120
Heat the crankshaft gear. Use a bearing heater oven (CAS-10133).
STEP 121
Install the key and the heated crankshaft gear on the crankshaft.
A CAUTION Always wear asbestos gloves to prevent burning your hands when handling heated parts.
STEP 122
Make sure that the timing mark on the gear is on the outside.
STEP 123
Make sure that the bearing liner bores are clean.
Install the main bearing liners.
NOTE: Make sure that the liner locks are aligned when installing the liners. Slide the liners in position.
Never push on the center of the liners.
Lubricate the bearing liners. Use clean engine oil.
…