INSTANT DOWNLOAD (add to cart)
Kobelco SK045, SK045-2, SK050, SK40SR, SK50SR, SK40SR-2, SK45SR-2 Workshop Repair & Service Manual
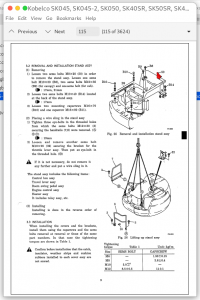
Complete digital official shop manual contains service, maintenance, and troubleshooting information for the Kobelco SK045, SK045-2, SK050, SK40SR, SK50SR, SK40SR-2, SK45SR-2 Hydraulic Excavators. Diagnostic and repair procedures are covered in great detail to repair, maintain, rebuild, refurbish or restore your vehicle like a professional mechanic in local service/repair workshop. This cost-effective quality manual is 100% complete and intact as should be without any missing pages. It is the same factory shop manual used by dealers that guaranteed to be fully functional to save your precious time.
This manual for Kobelco SK045, SK045-2, SK050, SK40SR, SK50SR, SK40SR-2, SK45SR-2 Hydraulic Excavators is divided into different sections. Each section covers a specific component or system and, in addition to the standard service procedures, includes disassembling, inspecting, and assembling instructions. A table of contents is placed at the beginning of each section. Pages are easily found by category, and each page is expandable for great detail. It is in the cross-platform PDF document format so that it works like a charm on all kinds of devices. You do not need to be skilled with a computer to use the manual.
“SK45SR-2 (S5PJ0001E).pdf”
Kobelco SK45SR-2 Hydraulic Excavators Shop Manual; 654 pages
“SK045,SK045-2,SK050 (S5PY0002E).pdf”
Kobelco SK045, SK045-2, SK050 Shop Manual; 532 pages
“SK40SR,SK50SR (S5PH0001E).pdf”
Kobelco SK40SR,SK50SR Hydraulic Excavators Shop Manual; 774 pages
“SK40SR-2,SK45SR-2 (S5PJ0002E).pdf”
Kobelco SK40SR-2, SK45SR-2 Hydraulic Excavators Shop Manual; 704 pages
EXCERPT:
3. REMOVAL AND INSTALLATION
3.1 GENERAL PRECAUTIONS
• Remove and install it in clean place.
• Before removing, clean the outside, particularly around the hydraulic oil port, and remove coating on the joints of each part with wire brush, etc.
• Wash and clean the removed parts with light oil.
• Put matchmark on the required parts to make the installation easier.
3.2 REMOVAL (REFER TO FIG. 2)
1) Fix the mounting flange (3) of the pump in a vise with the flange facing downward.
The aluminum plate, copper plate, etc. should be applied on the vice.
2) Loosen socket bolt (9), and remove it together with plain washer (10).
3) Remove the cover (1) straight up and off.
4) Remove the seal plate {7) and back-up (8).
5) Remove out the pressure plate (6).
6) Before removing, put matchmark on the end face of drive gear (4) and driven gear (5).
• Remove the drive gear (4) and driven gear (5).
7) Remove pressure plate (6).
• Remove it vertically in the shaft direction.
8) Identify the difference between the cover side and the flange side of the gear plate (2).
• The dowel pin on the gear plate (2) is press-fitted, so don’t remove it.
9) Remove seal plate (7) and back-up (8) from the mounting flange (3).
10) Turn over the mounting flange (3) and remove snap ring (12) and oil seal (11), too.
3.3 CHECK AND MAINTENANCE
Check the removed parts for possible damage and change in color and wash them with light oil. But rubber items must not be immersed in light oil.
Perform the following inspection, and replace the damaged parts with new ones.
1) Gear plate
The gear pump is designed in order to be operated under the condition where the tooth
tip contacts the body and is familiarized to achieve high volume efficiency. So the gear
pump operated once has contact trace to the suction part.
The allowable contact trace length is 1/2 or less than that of internal circumference of gear hole. And the allowable contact trace depth a is approx. 0.05mm. The depth a over 0.12mm is considered to be caused by the wear of shaft or bearing.
• The pump assy with a depth “a” of contact trace is 0.12mm or more should be replaced with a new one.
…