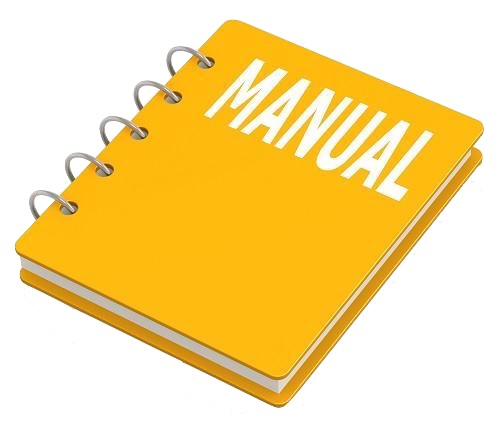
INSTANT DOWNLOAD (add to cart)
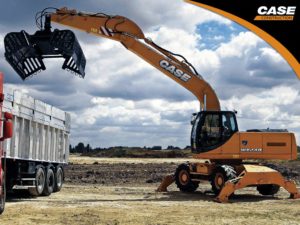
3,360 pages, bookmarked, Searchable, Printable, high quality PDF
9_91260_FR – Case WX210, WX240 PELLE HYDRAULIQUE Manuel de réparations.pdf
9_91270_EN – Case WX210, WX240 HYDRAULIC EXCAVATOR Service Manual.pdf
9_91280_DE – Case WX210, WX240 HYDRAULIKBAGGER Reparatur Handbuch.pdf
9_91290_SP – Case WX210, WX240 ESCAVADORA HIDRAULICA Manual de reparación.pdf
9_91300_IT – Case WX210, WX240 ESCAVATORE IDRAULICO Manuale per le riparazioni.pdf
Complete digital official shop manual contains service, maintenance, and troubleshooting information for the Case WX210, WX240 Hydraulic Excavator. Diagnostic and repair procedures are covered in great detail to repair, maintain, rebuild, refurbish or restore your Case WX210, WX240 Hydraulic Excavator like a professional mechanic in local service/repair workshop. This cost-effective quality manual is 100% complete and intact as should be without any missing pages. It is the same factory shop manual used by dealers that guaranteed to be fully functional to save your precious time.
This manual for Case WX210, WX240 Hydraulic Excavator is divided into different sections. Each section covers a specific component or system and, in addition to the standard service procedures, includes disassembling, inspecting, and assembling instructions. A table of contents is placed at the beginning of each section. Pages are easily found by category, and each page is expandable for great detail. It is in the cross-platform PDF document format so that it works like a charm on all kinds of devices. You do not need to be skilled with a computer to use the manual.
EXCERPT:
ELECTRONICS WX210 – WX240
Description
The two diagrams show the characteristics for the left and right joystick.
The characteristics of the Y-axis show the forward and reverse movement of the joystick handle and the change in digit value in relation to the angular deflection.
The characteristics of the X-axis show the transverse movement of the joystick handle.
Digit output starts at a joystick handle deflection of >0.7°.
In the X- and in the Y-axis, 512 digits are put out in the event of full deflection from the zero position.
Functioning principle of joysticks and pedals
Description
The joysticks are manually controlled pulse generators that permit the handle to be swivelled in any direction. The swivelling / pedal movements are picked up by sensors and put out via the interfaces as digital signals.
Joystick/pedal position detection and evaluation
The position of the movement axes is detected contact-free by Hall-effect sensors. Two Halleffect sensors per movement axis are used to ensure that the joystick operates correctly. The plausibility control of the signals is based on redundant signal evaluation, i.e. the internal microcontroller computes from the measured value of a Hall-effect sensor the probable value of the other sensor and then compares the computed with the measured value. If the difference between the two values exceeds a defined tolerance window, a troubleshooting routine comes into force.
During this process, all joystick and pedal functions are deactivated and a re-start of the unit is initiated.
The position of the joystick handle, i.e. the angular deflection into one or more directions, is registered in the same way for all joysticks. Four Halleffect sensors (two for X-direction and two for Ydirection) are mounted on a fixed p.c. board in the joystick housing. An annular magnet is attached to the articulated cardan joint at the top of which the joystick handle is located. On deflection of the joystick handle into one direction, the distance of the annular magnet from the sensors located in movement direction is reduced or increased. The resulting changes in the output voltages of the
Hall-effect sensors are converted by the controller into a digital value and can thus be further processed.
The definitive output signal results as a digital value from conversion, amplification and calibration.
Temperature compensation
Temperature compensation is used to reduce the unavoidable influencing of the signals in their digital / analog conversion through changes in ambient temperature. This compensation is executed subsequent to the A/D conversion in the microcontroller by a software program, with the actual ambient temperature being ascertained by an integrated temperature sensor and used for computation purposes. This procedure ensures high stability of the output signals, irrespective of fluctuations in ambient temperature, in a broad temperature range from -40°C to +85°C.
Power supply
The power supply of the controller is designed for an input voltage ranging from 8V to 30V DC.
It supplies the electronic system with a controlled voltage of 5V.
The 5V supply is monitored by a reset controller. If the supply voltage falls below 4.5V, the reset controller generates a reset signal that resets the supervisory controller (SC) directly. With the resetting of the SC, the main controller (MC) is also automatically reset; it is kept in this state until the SC goes through its initialization procedure again.
Only then is the MC released from the reset status by the SC.
Reverse voltage protection
Joystick/pedals have reverse voltage protection at the inputs. In addition, the inputs of the supply
voltage and the outputs of the circuit are protected against positive and negative voltage peaks by
600W suppressor diodes.
…