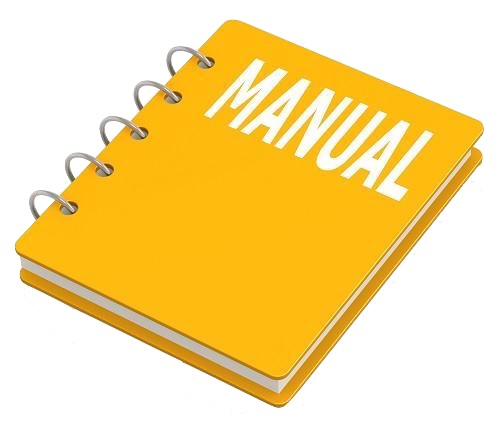
INSTANT DOWNLOAD
Complete digital official shop manual contains service, maintenance, and troubleshooting information for the Caterpillar 3126B, 3126E Engine. Diagnostic and repair procedures are covered in great detail to repair, maintain, rebuild, refurbish or restore your 3126 Engine like a professional mechanic in local service/repair workshop. This cost-effective quality manual is 100% complete and intact as should be without any missing pages. It is the same factory shop manual used by dealers that guaranteed to be fully functional to save your precious time.
This manual for Caterpillar 3126B, 3126E Engine is divided into different sections. Each section covers a specific component or system and, in addition to the standard service procedures, includes disassembling, inspecting, and assembling instructions. A table of contents is placed at the beginning of each section. Pages are easily found by category, and each page is expandable for great detail. It is in the cross-platform PDF document format so that it works like a charm on all kinds of devices. You do not need to be skilled with a computer to use the manual.
MANUAL LIST (376 MB PDF):
KENR6698 – Schematic (3126B Industrial Engine Electrical System)
RENR2242 – Schematic (3126B Marine Engine Electrical System)
RENR2243 – Troubleshooting (3126B Marine Engines)
RENR2247 – Specifications (3126B Marine Engine)
RENR2248 – Systems Operation (3126B Marine Engine)
RENR2248 – Testing & Adjusting (3126B Marine Engine)
RENR2249 – Disassembly & Assembly (3126B Marine Engine)
SEBU7242 – Operation & Maintenance Manual (3126B Marine Engine)
SENR9577 – Schematic (3126B Engine for Claas Combine Applications Electrical System)
SENR9579 – Specifications (3126B Engine for Caterpillar Built Machines)
SENR9580 – Systems Operation (3126B Engines for CaterpillarBuilt Machines)
SENR9580 – Testing & Adjusting (3126B Engines for CaterpillarBuilt Machines)
SENR9581 – Disassembly & Assembly (3126B Engines for Caterpillar Built Machines)
SENR9587 – Specifications (3126B Industrial Engine)
SENR9588 – System Operation (3126B Industrial Engine)
SENR9588 – Testing & Adjusting (3126B Industrial Engine)
SENR9589 – Disassembly & Assembly (3126B Industrial Engine)
SENR9590 – Schematic (3126B Industrial Engine Electrical System)
SENR9591 – Troubleshooting (3126B Industrial Engine)
SENR9631 – Systems Operation (3126E Truck Engines)
SENR9631 – Testing and Adjusting (3126E Truck Engines)
SENR9632 – Specifications (3126E Truck Engine)
SENR9633 – Disassembly and Assembly (3126E On-highway Engine)
SENR9637 – Troubleshooting (3126E On-highway Engine)
SENR9638 – Schematic (3126E Truck Engine Electrical System)
RENR1368 – Schematic (3126B and 3126E On-highway Engines).pdf
Cooling System (3126B & 3126E).pdf
Fuel System (3126B & 3126E).pdf
Intake, Exhaust & Turbocharger (3126B & 3126E).pdf
Lubrication (3126B & 3126E).pdf
Mechanical (3126B & 3126E).pdf
Troubleshooting (3126B & 3126E).pdf
…
CD-ROM (3126B & 3126E Truck Engines) RENR1361-11
Service Manual RENR1360
3126B and 3126E Truck Engines
BKD1-Up, G3E1-Up, DPF1-Up, 1AJ1-Up, 8YL1-UP, CKM1-Up, CRP1-Up, 7AS1-UP, 8SZ1-UP, 9SZ1-Up
EXCERPT:
Binder SENR2300 14.26 6.43
Binder Label RENR1359 03 .30 .30
Safety SENR2995 03 .30 .05
Service Manual Contents RENR1361 05 .30 .30
Torque Specifications SENR3130 06 3.40 2.00
Engine Index Tab SENR2870 .30 .30
Specifications 3126B and 3126E Truck Engines RENR1270 02 6.50 5.28
Systems Operations, Testing & Adjusting 3126B and 3126E Truck Engines RENR1271 02 15.50 8.06
Disassembly & Assembly 3126B and 3126E Truck Engines RENR1369 02 15.50 8.06
Service Manual Bendix Air Compressors SENR6455 00 6.50 5.28
Service Manual Midland Air Compressors SENR7594 03 6.50 5.28
Service Manual Bendix Air Compressors SENR5122
Service Manual Wabco Air Compressors RENR2314 00 3.40 2.78
Attachments Index Tab SENR2876 .30 .30
Owner’s Manual Caterpillar Driver Information Display SEBU6875 04 9.52 8.88
Screen Map Cat ID Screen Map SENR6503 04 3.40 2.78
Service Manual PTO Installation & Application
Instruction
RENR1282 00 15.50 8.06
Troubleshooting Index Tab SENR3987 .30 .30
Electrical Schematic 3126E Truck Engine SENR9675
Electrical Schematic 3126B and 3126E Truck Engines RENR1368 02 15.50 12.53
Troubleshooting 3126B and 3126E Truck Engines RENR1367 01 39.70 32.21
Maintenance Index Tab SENR2874 .30 .30
Operation & Maintenance 3126B and 3126E Truck Engines SEBU7011
…
Introduction
View Image
Illustration 1 g00457847
Diagram of components for the HEUI fuel system
(1) Unit injector hydraulic pump
(2) Oil flow to engine
(3) Oil filter
(4) Engine oil pump
(5) Oil cooler
(6) IAP sensor
(7) Injectors
(8) Fuel supply rail
(9) Fuel pressure regulator
(10) IAP control valve
(11) Fuel filter
(12) Fuel tank
(13) Back of cam gear
(14) Speed/timing sensors
(15) ECM
(16) Boost pressure sensor
(17) Accelerator pedal
(18) Accelerator pedal position sensor
(19) Batteries
(20) Coolant temperature sensor
(21) Data link
(22) Exhaust brake relay
(23) Inlet air temperature sensor
(24) Transmission relay
(25) Vehicle speed sensor
(26) Inlet air heater relay
(27) Inlet air heater lamp
(28) Fast idle lamp
(29) Check engine lamp
(30) Speedometer and tachometer
(31) Cruise ON/OFF switch and Cruise SET/RESUME switch
(32) PTO ON/OFF switch and SET/RESUME switch
(33) Service brake switches
(34) Neutral and clutch switches
(35) Fuel transfer pump
The operation of the Hydraulic Electronic Unit Injector (HEUI) fuel system is completely different from any other type of fuel system that is actuated mechanically. The HEUI fuel system is completely free of adjustment. Adjustments to the components that are mechanical can not be made. Changes in performance are made by installing different software in Engine Control Module (ECM) (15) .
This fuel system consists of six basic components:
Hydraulic Electronic Unit Injector (HEUI) (7)
Engine Control Module (ECM) (15)
Unit injector hydraulic pump (1)
Injection Actuation Pressure Control Valve (10)
Fuel Transfer Pump (35)
Injection Actuation Pressure Sensor (6)
Note: The components of the HEUI fuel system are not serviceable. These fuel system components must not be disassembled. Disassembly will damage the components. If the components have been disassembled, Caterpillar may not allow a warranty claim or Caterpillar may reduce the warranty claim.
Component Description
Hydraulic Electronic Unit Injector
The HEUI fuel system utilizes a hydraulically actuated electronically controlled unit injector (7) .
All fuel systems for diesel engines use a plunger and barrel in order to pump fuel under high pressure into the combustion chamber. This fuel is pumped into the combustion chamber in precise amounts in order to control engine performance. The HEUI uses engine oil under high pressure in order to power the plunger. All other fuel systems use a fuel injection pump camshaft lobe in order to power the plunger. Because the HEUI is much different, a technician must use different troubleshooting methods.
The HEUI uses engine lubrication oil that is pressurized from 6 MPa (870 psi) to 27.5 MPa (4000 psi) in order to pump fuel from the injector. The HEUI operates in the same way as a hydraulic cylinder in order to multiply the force of the high pressure oil. By multiplying the force of the high pressure oil, the HEUI can produce injection pressures that are very high. This multiplication of pressure is achieved by applying the force of the high pressure oil to a piston. The piston is larger than the plunger by approximately six times. The piston that is powered by engine lubrication oil under high pressure pushes on the plunger. This engine lubrication oil under high pressure is called the actuation pressure of the oil. The actuation pressure of the oil generates the injection pressure that is delivered by the unit injector. Injection pressure is greater than actuation pressure of the oil by approximately six times.
Low actuation pressure of the oil results in low injection pressure of the fuel. During conditions of low speed such as idle and start, low injection pressure is utilized.
High actuation pressure of the oil results in high injection pressure of the fuel. During conditions of high speed such as high idle and acceleration, high injection pressure is utilized.
There are many other operating conditions when the injection pressure is between the minimum and the maximum. Regardless of the speed of the engine, the HEUI fuel system provides infinite control of injection pressure.
Engine Control Module (ECM)
Engine Control Module (ECM) (15) is located on the left side of the engine. The ECM is a powerful computer that provides total electronic control of engine performance. The ECM uses data from engine performance that is gathered by several sensors. Then, the ECM uses this data in order to make adjustments to the fuel delivery, injection pressure and injection timing. The ECM contains programmed performance maps (software) in order to define horsepower, torque curves and rpm. This software is commonly called the personality module.
Some engines use Engine Control Modules (ECM) (15) with a replaceable computer chip. The software has already been installed in the replaceable computer chip. The 3126B and 3126E diesel truck engines do not have a replaceable personality module. The 3126B and 3126E diesel truck engine’s personality module are a permanent part of the ECM. The 3126B and 3126E diesel truck engine’s personality module can be reprogrammed. Reprogramming of the personality module requires the use of Caterpillar Electronic Technician (Cat ET). The flash function of Cat ET will be used during the reprogramming.
ECM (15) logs faults of engine performance. Also, the ECM is capable of running several diagnostic tests automatically when the ECM is used with an electronic service tool such as the Cat ET.
Unit injector hydraulic pump
…
INJECTOR SYNCHRONIZATION
Injector synchronization is setting of all injector racks to a reference position so each injector gives the same amount of fuel to each cylinder. This is done by setting each injector to the same position while control linkage is in a fixed position (called the synchronizing position). Control linkage is at synchronizing position when cylinder No. 1 injector is at fuel shutoff. Since injector No. 1 is reference point for other injectors, no synchronizing adjustment is made to injector No. 1.
Always synchronize an injector when it has been removed and reinstalled.
1. Turn off engine and shut off engine’s electrical system. Remove fuel shutoff solenoid to allow injector rack control linkage to move freely during injector synchronization. Remove fuel shutoff solenoid using Spanner Wrench (4C4734). See Fig. 2.
2. Remove valve cover from intake manifold. Remove 4 bolts and cylinder No. 1 rocker arm assembly. See Fig. 3.
Fig. 3: Removing Fuel Shutoff Solenoid
3. Apply a small amount of clean engine oil to top of injector. Install Injector Spring Compressor (1U6675) to cylinder head and injector. See Fig. 4. Tighten bolt on Spring Compressor (1V6675) which is threaded into cylinder head hole for rocker arm assembly. This compresses injector. Tap lightly with a soft hammer on spring compressor directly above injector to ensure free movement of injector rack bar.
…