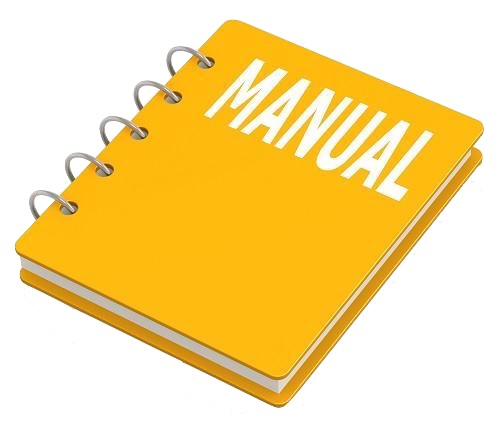
INSTANT DOWNLOAD (add to cart)
Complete workshop & service manual with electrical wiring diagrams for Caterpillar Telehandler TL642C, TL943C. It’s the same service manual used by dealers that guaranteed to be fully functional and intact without any missing page.
Caterpillar Caterpillar Telehandler TL642C, TL943C service & repair manual (including maintenance, overhaul, disassembling & assembling, adjustment, tune-up, operation, inspecting, diagnostic & troubleshooting…) is divided into different sections. Each section covers a specific component or system with detailed illustrations. A table of contents is placed at the beginning of each section. Pages are easily found by category, and each page is expandable for great detail. The printer-ready PDF documents work like a charm on all kinds of devices.
FILELIST:
31200162 – JLG Drive Axle Supplemental Repair Manual (Models 3507, 3508, 3509, 3512, 3513, 4007, 4008, 4009, 4012, 4013, 4017, G6-42A, 642, TF6-42, TL642, & TL642C).pdf
31200239 – JLG Drive Axle Supplemental Repair Manual (Models G9-43A, G10-43A, 943, 1043, 1055, 1255, TL943, TL943C, TL1055C, TL1255C).pdf
31200747 (SEBU9289) – Operation & Maintenance Manual (Models TL642C, TL943C).pdf
31200794 – Service Manual (Models TL642C, TL943C).pdf
31200820 (SSBU9289) – Manual del operador y de mantenimiento (Modelos TL642C, TL943C).pdf
31200821 (SPBU9289) – Manual de Operação e Manutenção (Modelos TL642C, TL943C).pdf
31200829 – Electrical Schematic (Models TL642C & TL943C).pdf
31200830 – Electrical Schematic (Models TL642C & TL943C).pdf
…
EXCERPT:
8.8.3
Cylinder Pressure Checking
Attach a 5000 psi (345 bar) gauge to the test port on the P1 port on the hydraulic manifold to check the system pressure. For more information, refer to Section 8.4.1,
“Hydraulic Pressures.”
Note: If a hydraulic cylinder pressure is greater than the main control valve pressure, increase the main control valve pressure by adjusting the main relief. Generally, one half turn clockwise will be adequate to check an individual circuit. Activate the circuit and if pressure is obtained turn the main relief counter clockwise one half turn. Re-check the main relief setting and adjust if necessary.
…