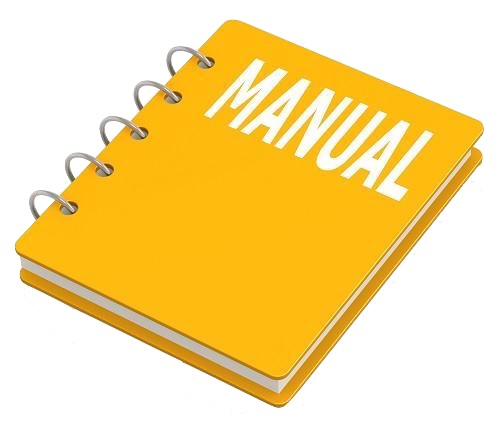
INSTANT DOWNLOAD (add to cart)
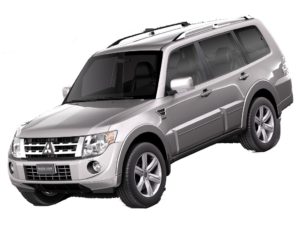
Complete workshop & service manual with electrical wiring diagrams for Mitsubishi Pajero/Montero, Pajero/Montero Sport 1982-2006. It’s the same service manual used by dealers that guaranteed to be fully functional and intact without any missing page.
This Mitsubishi Pajero/Montero, Pajero/Montero Sport 1982-2006 service & repair manual (including maintenance, overhaul, disassembling & assembling, adjustment, tune-up, operation, inspecting, diagnostic & troubleshooting…) is divided into different sections. Each section covers a specific component or system with detailed illustrations. A table of contents is placed at the beginning of each section. Pages are easily found by category, and each page is expandable for great detail. The printer-ready PDF documents work like a charm on all kinds of devices.
3.8 GB PDF, 10,000+ pages, bookmarked, Searchable, Printable, high quality PDF
’91-’02 Pajero_Montero (EN-DE-ES-FR)
’04 Montero, Montero Sport
’91-’03 Pajero
’91-’99 Pajero
’01-’03 Pajero_Montero (EN-DE-ES-FR)
’92-’95 Montero.pdf
’00-’03 Pajero Pinin.zip
’99-’02 Pajero Sport.zip
’92 Montero.pdf
’03 NP Pajero
’97-’99 Montero Sport.pdf
’01 Pajero (EN-DE-ES-FR)
’01-’02 Pajero
’01-’03 Pajero
’01-’03 Pajero_Montero
’03 Montero
’06 Montero
’93 Montero
’98 Montero
’98 Pajero Sport
’99 Pajero Sport
’99-’01 Pajero Sport
…
EXCERPT:
GROUP INDEX
General . . . 00
Engine . . . 11
Engine Lubrication . . . 12
Fuel . . . 13
Engine Cooling . . . 14
Intake and Exhaust . . . 15
Engine Electrical. . . 16
Engine and Emission Control . . . 17
Automatic Transmission . . . 23
Propeller Shaft . . . 25
Front Axle . . . 26
Rear Axle . . . 27
Wheel and Tire . . . 31
Power Plant Mount . . . 32
Front Suspension . . . 33
Rear Suspension . . . 34
Alphabetical Index . . . Index
…
FUEL TANK ROLLOVER VALVE ASSEMBLY CHECK
1. Shake the fuel tank rollover valve assembly up and down to check if the float inside the fuel tank rollover valve assembly is not seized. If seized, replace the fuel tank rollover valve assembly.
2. Obtain a container, which is full of water.
3. Invert the fuel tank rollover valve assembly, and submerge it slowly in the water while placing your fingers over the nozzle.
4. Check that no more air bubbles appears from the fuel tank rollover valve assembly, and withdraw it slowly.
5. Open the fuel tank rollover valve assembly nozzle. If no water flows out from the nozzle aperture, the valve is normal. If water flows out, the float or spring inside the fuel tank rollover valve is defective. Replace the fuel tank rollover valve assembly.
…
MAKE: Mitsubishi
YEAR: 1983 1984 1985 1986 1987 1988 1989 1990 1991 1992 1993 1994 1995 1996
MODEL: Pick-ups, Montero, Pajero
Complete coverage for your Mitsubishi Pick-ups & Montero for 1983 thru 1996 covering 2WD & 4WD models with gasoline engines Pick-ups (1983 thru 1996) Montero (1983 thru 1993):
–Routine Maintenance
–Tune-up procedures
–Engine repair
–Cooling and heating
–Air Conditioning
–Fuel and exhaust
–Emissions control
–Ignition
–Brakes
–Suspension and steering
–Electrical systems
–Wiring diagrams
’84.altenate.pdf
’83.pdf
’83-’96 Pick-ups, Montero.pdf
’84.pdf
’87
’89
’91
…
EXCERPT:
Tests With Codes.pdf
L-Wiring Diagrams.pdf
Electrical Component Locator.pdf
Cruise Control System.pdf
Engine Overhaul Procedures.pdf
Waveforms Injector Pattern Tutorial.pdf
3.0L V6.pdf
Transfer Case.pdf
AC Compressor Servicing.pdf
Vacuum Diagrams.pdf
Symptom Check List.pdf
Emission Control Visual Inspection Guidelines.pdf
Wiring Diagrams.pdf
Steering Column Switches.pdf
AC Heater System Manual.pdf
Alternator And Regulator.pdf
Maintenance Info.pdf
System Wiring Diagrams.pdf
Drive Axle Rear Non Integral.pdf
Heater System.pdf
Transmission Servicing At.pdf
Engine Cooling Fan.pdf
Remove Install Overhaul.pdf
Brake System.pdf
Scheduled Services.pdf
Instrument Panel.pdf
Specifications.pdf
Starter.pdf
System Component Tests.pdf
Basic Testing.pdf
Maintenance Reminder Light Reset Procedures.pdf
Engine Systems Uniform Inspection Guidelines.pdf
Engine Vin Id.pdf
Service Indicator and Warning Lights.pdf
Drive Axle Front.pdf
Suspension Front 4Wd.pdf
Trouble Shooting.pdf
Wiring Diagram Symbols.pdf
Adjustments.pdf
Locking Hubs.pdf
Wheel Alignment Theory Operation.pdf
Drive Belt Routing.pdf
Suspension Uniform Inspection Guidelines.pdf
Electrical System Uniform Inspection Guidelines.pdf
Transmission Servicing Mt.pdf
How To Use System Wiring Diagrams.pdf
Wheel Alignment Specifications and Procedrues.pdf
Defogger Rear Window.pdf
Drivetrian Systems Uniform Inspection Guidelines.pdf
AC Heater System Uniform Inspection Guidelines.pdf
Wiper Washer System.pdf
Jacking and Hoisting.pdf
Brake System Uniform Inspection Guidelines.pdf
Gear Tooth Contact Patterns.pdf
AC Compressor Oil Checking.pdf
General Cooling System Servicing.pdf
Electrostatic Discharge Warning.pdf
Fuses and Circuit Breakers.pdf
Exhaust System Uniform Inspection Guidelines.pdf
Theory Operation.pdf
Riding Height Adjustment.pdf
Metric Conversions.pdf
AC System Precautions.pdf
Transmission Removal and Installation At.pdf
Tests Without Codes.pdf
Sensor Range Charts.pdf
Egr Function Testsing.pdf
Emission Application.pdf
Interference Verification Check For Ohc Engine.pdf
Anti Lock Bake Safety Precautions.pdf
Front Seat Belts.pdf
Trailer Hitch Weld Can Break.pdf
Computer Relearn Procedures.pdf
Front Safety Belt Buckle Release Button Can Break.pdf
Cooling System Specifications.pdf
Pre Alignment Checks.pdf
…
VALVE STEM OIL SEALS
Valve stem oil seals must be installed on valve stem. See Fig. 2. Seals are needed due to pressure differential at the ends of valve guides. Atmospheric pressure above intake guide, combined with manifold vacuum below guide, causes oil to be drawn into the cylinder.
Exhaust guides also have pressure differential created by exhaust gas flowing past the guide, creating a low pressure area. This low pressure area draws oil into the exhaust system.
Replacement (On Vehicle)
Mark rocker arm or overhead cam components for location.
Remove rocker arm components or overhead cam components. Components must be installed in original location. Remove spark plugs. Valve stem oil seals may be replaced by holding valves against seats using air pressure.
Air pressure must be installed in cylinder using an adapter for spark plug hole. An adapter can be constructed by welding air hose connection to spark plug body with porcelain removed.
Install adapter in spark plug hole. Apply a minimum of 140 psi (9.8 kg/cm ) to adapter. Air pressure should hold valve closed. If air pressure does not hold valve closed, check for damaged or bent valve. Cylinder head must be removed for service.
…