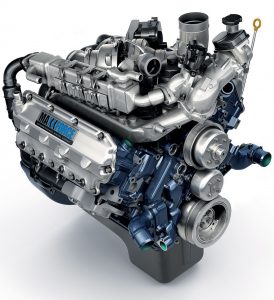
INSTANT DOWNLOAD
Complete digital official shop manual contains service, maintenance, and troubleshooting information for the International/Navistar VT275, D312, D360, DTA-360, DT360, VT365, D414, DT414, DT414B, D436, DT436, DT436B, T444E, D466, DT466, DT466B, DTI466, DTI466B, DT466C, DTI466C, DT466E, DT530, DT530E, HT530, DT570, HT570 Diesel Engines. Diagnostic and repair procedures are covered in great detail to repair, maintain, rebuild, refurbish or restore your vehicle like a professional mechanic in local service/repair workshop. This cost-effective quality manual is 100% complete and intact as should be without any missing pages. It is the same factory shop manual used by dealers that guaranteed to be fully functional to save your precious time.
This manual for International/Navistar VT275, D312, D360, DTA-360, DT360, VT365, D414, DT414, DT414B, D436, DT436, DT436B, T444E, D466, DT466, DT466B, DTI466, DTI466B, DT466C, DTI466C, DT466E, DT530, DT530E, HT530, DT570, HT570 Diesel Engines is divided into different sections. Each section covers a specific component or system and, in addition to the standard service procedures, includes disassembling, inspecting, and assembling instructions. A table of contents is placed at the beginning of each section. Pages are easily found by category, and each page is expandable for great detail. It is in the cross-platform PDF document format so that it works like a charm on all kinds of devices. You do not need to be skilled with a computer to use the manual.
FILELIST (549 MB PDFs):
EGES-210-1 – DT 466E, 530E, 466, 530 & HT 530 Diesel Engine Service Manual (Model Year 2000 & up)
EGES-215 – DT 466 & 530 Diesel Engine Diagnostic_Troubleshooting Manual (Service Manual)
EGES-235-2 – VT 365 Diesel Engine Service Manual (Model Year 2002 & 2003)
EGES-240 – VT 365 Engine Diagnostic_Troubleshooting Manual (Service Manual)
EGES-265-1 – DT 466, DT 570, HT 570 Engine Service Manual (2004 Emissions with EGR)
EGES-265-2 – DT 466, DT 570, HT 570 Diesel Engine Service Manual (2004 Model Year & above)
EGES-270 – DT 466, DT 570, HT 570 Diesel Engine Diagnostic_Troubleshooting Manual (Service Manual) (2005 June)
EGES-270-1 – DT 466, DT 570, HT 570 Diesel Engine Diagnostic_Troubleshooting Manual (Service Manual) (2004 Emissions with EGR)
EGES-295-2 – VT 365 Diesel Engine Service Manual (2004-2006 Model Years)
EGES-305-2 – VT 275 Engine Diagnostic_Troubleshooting Manual (Service Manual) (2006)
Advanced Electrical Technical Information.pdf
CGE-630-1 – Diagnostic Trouble Codes & Circuit Diagrams & Diamond Logic Control Ii Engine Applications.pdf
CGES-430-3 – DT_DTA-360 Diesel Engine Service Manual (1992-03).pdf
CGES-445-3 – DT_DTA-360 Diesel Engines Diagnostic Manual in International Trucks (1992-01).pdf
EGES-120-1 – T 444E Diesel Engine Service Manual (Model Years 1994-1997).pdf
EGES-125-1 – T 444E Diesel Engine_Vehicle Diagnostic Manual in International Trucks (1997-05).pdf
EGES-175-1 – DT 466E and International 530E Engine Diagnostic_Troubleshooting Manual for 4000 Series Trucks.pdf
EGES-190 – T 444E Diesel Engine_Vehicle Diagnostic Manual in International Trucks (1997-12).pdf
EGES-205 – T 444E Diesel Engine Service Manual (Model Years Late 1997-2003).pdf
EGES-211 – Manual de servicio para motores diesel DT-466E e International 530E (2000-12).pdf
EGES-300-1 – VT 275 Diesel Engine Service Manual (Model Year 2005 & up).pdf
Emissions – Diesel (Navistar T444E Elec Eng Ctrl).pdf
Ford 7.3 Direct Injection Turbocharged (DIT) Diesel Engine Features_Description_Service Features.pdf
GSS-1427 – 300 & 400 Series Diesel Engine & Fuel System Service Manual.pdf
EGED-256 – Diagnósticos del sistema de control electrónico International VT 365.pdf
EGES-210-1 – DT 466E, 530E, 466, 530 & HT 530 Diesel Engine Service Manual (Model Year 2000 & up).pdf
EXCERPT:
Service Diagnosis
Service diagnosis is a systematic procedure of investigation to be followed in order to locate and correct an engine problem. The engine is first considered as a complete unit in its specific application and then the problem is localized to components or systems; intake, exhaust, cooling, lubrication or injection. Testing procedures will then help analyze the source of the problem.
PREREQUISITES FOR EFFECTIVE DIAGNOSIS:
• Knowledge of the principles of operation for both the engine and application systems
• Knowledge to perform and understand all procedures in the diagnostic and service publications
• Availability of and the ability to use gauges and diagnostic test equipment
• Availability of the most current information for the engine application
Although the cause of an engine failure may be apparent, very often the real cause is not found until a repeat failure occurs. This can be prevented if specific diagnostic action is taken before, during and after engine disassembly and during engine assembly.
…
VALVE TRAIN: PUSH RODS, HYDRAULIC VALVE LIFTERS AND CAMSHAFT
Push Rods and Hydraulic Valve
Lifters
Operation
NOTE: As a general rule, hydraulic valve lifters should not require any service if they are operating quietly and functioning satisfactorily.
Figure 226 Valve Lifter Components
1. Lifter Body with Roller
2. Spring
3. Plunger
4. Plunger Body
5. Metering Valve
6. Push Rod Seat
7. Retainer
Lube oil from the oil gallery is supplied to the lifters through a hole in the side of the lifter body that indexes with a groove and hole in the lifter plunger. Oil is then metered past the oil metering valve, up through the push rods and onto the valve levers.
When the lifter begins to roll up the cam lobe, the metering valve is held against its seat in the plunger body by the spring. This action traps the oil in the base of the lifter body below the plunger. The plunger body and lifter body then rise as a unit, pushing the push rod up in order to open the valve. The spring force exerted on the plunger through the valve lever and push rod causes a slight amount of leakage between the plunger and lifter body.
“Leak down” is the term used to describe this leakage. Leak down allows a slow escape of trapped oil in the base of the lifter body. As the lifter rides down the other side of the cam lobe and reaches the base circle or “valve closed” position, the plunger spring quickly moves the plunger back up to its original position. This movement causes the check valve to open against the check valve spring and allows oil to be replenished from the oil gallery. This restores the lifter to zero lash.
…
Special Remarks for Diagnostics Verification:
1. Always use proper probes in order to reduce any chance of damaging the connector pins;
2. When checking short-circuit to ground, proceed as follows:
2a. Turn ignition switch off;
2b. Disconnect the connectors you want to check. For testing a sensor, disconnect the harness connector; for testing a harness connector from ECM, disconnect also the connector(s) from sensor or sensors;
2c. Identify the pins to be checked;
2d. Visually inspect the pins;
2e. Adjust the multitester for resistance checking;
2f. Place the multitester probe on the pin to be verified and touch the engine block with the other probe.
3. Check for corrosion signs, bent pins or moisture presence on sensor or harness connector that could potentially cause the engine to failure;
4. 4. Inspect the fuel injector wire harness terminal nuts and check that there is no short circuit to ground between the wires and any metallic part near cylinder head cover that could generate failures on engine; after assembling the wire harness, tighten the nuts properly;
5. 5. Check battery condition (oxidized poles/cable terminals, cabling with damaged insulation, or low charge) that could generate failures on engine;
6. 6. Check the alternator’s voltage regulator that, in case of abnormal function, could generate an excessive or insufficient charge for the battery, causing failures on engine; the battery voltage shall be within the parameters specified by the vehicle manufacturer.
INSTANT DOWNLOAD