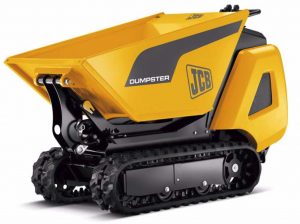
Pages from 9803-1400 – JCB Attachments Service Manual
JCB Manual Pack
FILELIST:
9801-9907 – JCB VLT Lighting Tower Operator Manual.pdf
9803-1400 – JCB Attachments Service Manual.pdf
9803-9320 – JCB Dumpster TD7, TD10 Service Manual.pdf
9803-9430 – JCB ZT 20D Service Manual.pdf
9803-9570 – JCB Dumpster HTD5 Service Manual.pdf
9803-9985 – JCB CP1 & CP2 Digital Control Panels Service Manual.pdf
9806-2150 – JCB Industrial Engine Systems LPG 3.0 Engine Workshop Manual.pdf
9806-3080 – Lombardini indirect injection Diesel engines type 15LD225, 15LD315, 15LD350, 15LD400, 15LD440 Workshop Manual.pdf
9806-4005a – Lombardini Gearbox Workshop Manual.pdf
9806-4060 – Lombardini CHD series Engine Workshop Manual.pdf
9806-4061 – Lombardini LDW 1503, LDW 1603, LDW 2004, LDW 2004/T, LDW 2204, LDW 2204/T CHD Use & Maintenance Manual.pdf
9806-4650 – Installation, Service & Maintenance Manual for STAMFORD BC Range of Generators.pdf
9806-4750 – Himoinsa Generators Self-regulating Alternators Series Eco-ECP Operating & Maintenance Instructions.pdf
9806-4800 – JCB Digital Control Panel Operators Manual.pdf
9806-5000 – Sincro SK160 4 Poles Brushless Alternators Use and Maintenance Manual.pdf
9811-1870 – Generator Set – G50R, G80R, G55X, G55QX, G66X, G66QX, G88X, G88QX, G110X, G110QX, G120X, G120QX Operator Manual.pdf
9811-2800 – Generator Set – G17, G17Q, G20R, G22, G22Q, G30R, G33, G33Q Operator Manual.pdf
9811-2850 – Generator Set – G144, G144Q, G175, G175Q, G220, G220Q, G130R, G160R, G200R Operator Manual.pdf
9811-2900 – Generator Set – G330, G330Q, G350, G350Q, G380, G380Q, G400, G400Q, G400, G440Q, G550, G550Q Operator Manual.pdf
9811-4550 – Generator Set – Models G8X to G45QX Operator Manual.pdf
9811-4600 – Generator Set – Models G60RX to G115QX Operator Manual.pdf
9811-4650 – Generator Set – Models G130RX to G220QX Operator Manual.pdf
9811-4700 – Generator Set – Models G250RX to G600X Operator Manual.pdf
9811-5050 – Lighting Tower LT9 Operator Manual.pdf
9821-1950 – Lighting Tower LTM9 Operator Manual.pdf
EXCERPT:
Service Manual Dumpster TD7, TD10
General Information 1
Care & Safety 2
Routine Maintenance 3
Attachments A
Body & Framework B
Electrics C
Controls D
Hydraulics E
Gearboxes F
Track & Running Gear J
Engine L
…
Hydraulic Fluid Quality
Construction machinery uses a large volume of fluid in the hydraulic system for power transmission, equipment lubrication, rust prevention and sealing.
According to a survey conducted by a pump manufacturer, seventy per cent of the causes of problems in hydraulic equipment were attributable to inadequate maintenance of the quality of the hydraulic fluid.
Therefore, it is obvious that control of the quality of the hydraulic fluid helps prevent hydraulic equipment problems and greatly improves safety and reliability. Furthermore from an economic angle it extends the life of the hydraulic fluid if quality is maintained.
Effects of Contamination
Once inside the system, hydraulic circuit contaminants greatly effect the performance and life of hydraulic equipment. For example, contaminants in a hydraulic pump develop internal wear to cause internal leakage and hence lower discharges. Wear particles generated will circulate with the hydraulic fluid to cause further deterioration in the performance of this and other equipment.
Contaminants also enter principal sliding sections of the equipment causing temporary malfunction, scuffing, sticking and leakage and can lead to major problems.
The main contaminants can be classified as follows:-
1 Solid Particles – sand, fibres, metallic particles, welding scale, sealing materials and wear particles etc.
…